Eric Arts, PhD, could never have imagined that a global pandemic would emerge just a few short months after cutting the ribbon for the Imaging Pathogens for Knowledge Translation (ImPaKT) Facility. Less than a year later, this lab has been at the forefront in understanding SARS-CoV-2, the virus that causes COVID-19, and finding new ways to prevent transmission.
In its design, partnerships between researchers and industry were anticipated, but with COVID-19, this vision rapidly became reality.
The advanced biocontainment lab in ImPaKT has facilitated expertise to help companies test and tweak the anti-viral properties of their products against SARS-CoV-2 to ensure the best protection for consumers.
“We are so grateful to have this facility during this time. ImPaKT allows us to safely study this virus under a variety of different conditions using state-of-the art imaging equipment,” said Arts, professor at Schulich Medicine & Dentistry and executive director at ImPaKT.
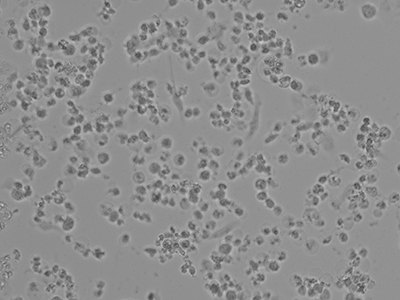
Image of SARS-CoV-2, the virus that causes COVID-19, infecting cells. Image courtesy: Western ImPaKT facility
ImPaKT is the only facility of its kind in Canada and houses sophisticated imaging technology within a biosafety 3 lab – giving researchers the tools to understand how viruses and bacteria behave and are transmitted in different environments.
For companies like ViRepel and CpK Interior Products, the testing done at ImPaKT has allowed them to launch products that reduce the amount of the COVID-19 virus that can survive on surfaces – making the environments that we move through on a daily basis safer.
ViRepel’s product is a thin adhesive film containing antimicrobial copper that can be placed on high-touch surfaces like door handles and in retail spaces.
“Copper has been known for centuries to have beneficial health properties,” said ViRepel co-founder and president Patrick Rodmell. “In more recent times, with the evolution of science, we now understand how copper works against bacteria and viruses. We wanted to see how that translated to the novel coronavirus and ImPaKT was the perfect partner to help us explore this.”
In the ImPaKT Facility, researchers put the product through a series of rigorous tests involving constant contact of the material with the virus. They found that the material was able to kill the virus at an extremely accelerated pace compared to normal surfaces.
Similarly, when Fiat-Chrysler subsidiary CpK Interior Products Inc. was looking for ways to make the interiors of vehicle cabins safer, they came to ImPaKT researchers to test the antiviral properties of a range of different materials.
“Vehicles are rarely single-user anymore, and provide a very confined space for virus to accumulate through activities like ride-sharing,” said Greg Farrar, PhD, head of R&D and advanced engineering manager at CpK Interior Products. “This initiative is really aimed at making car interiors healthier for people.”
Arts says with CpK, it was important to mimic real-world environments with their testing because the product has a very specific application. The product was tested first to determine its antiviral properties, and then looking at how it performs in “real life” exposure to the virus in vehicles by testing how the material kills aerosolized virus settling on surfaces using a specialized chamber in ImPaKT.
“For CpK we began by testing a series of different materials and coatings on materials, and moved forward only the ones that worked best,” said Arts. The product is anticipated to be rolled out into a future vehicle.
For both products, the goal is the same – to halt the transmission of the virus on surfaces and to allow people to feel more comfortable in the environments that they are in.